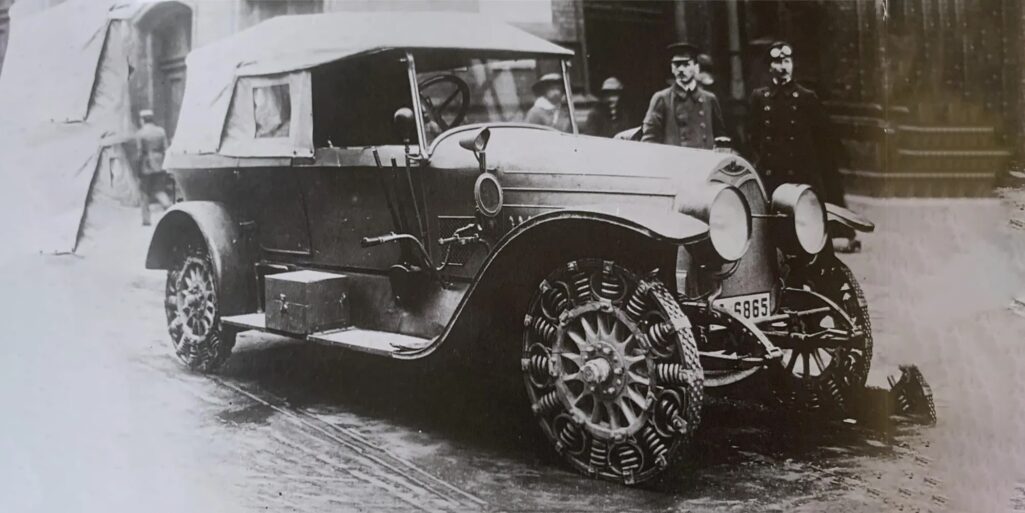
For a long time, the overall look of an automobile wheel with a central disk and an air-filled tire has been established and has shown to be successful. However, attempts are undertaken regularly to dramatically redesign such a framework to improve its technical or economic qualities: the so-called airless tire, which has elastic parts but no pressurized gas.
The first options for airless tires arrived towards the beginning of the century. Often, the appearance of such undertakings was due to a lack of materials. Designers attempted to replace difficult-to-access and costly rubber with more profitable wood or metal. To date, the deficit problem has been solved, and subsequent developments are motivated only by a desire to increase the chassis’s performance.

Earlier airless tire designs typically had a metal disk and an outer rim with tread, joined by a series of springs of different forms and arrangements. Cylindrical or leaf springs were utilized at various eras. These ideas typically handled the problems, but they proved to be excessively complicated and difficult to use. As a result, they did not appear in a huge series and were not widely distributed.
Consider some of the current styles of airless tires that have been developed in recent decades. As a result, Resilient Technologies’ Airless: Resilient NPT project attracted widespread attention in the past. It has been under development since 2002, and testing began towards the end of the decade. American engineers built a really unique design using current polymeric materials that were not available in the distant past.
The Airless: Resilient NPT tire is a single design that consists of a central mounting disk, an exterior rim with tread, and a specific frame that connects them. The latter is a lattice construction composed of irregular hexagons and trapezoids. The weight of the vehicle is split between the rim and grille, which are pretty stiff. At the same time, the structure’s flexibility allows it to absorb shock.

Michelin created the Tweel (Tire + Wheel) tire idea in 2005. The core disk and outer rim are linked in this design by V-shaped “spokes” that span the whole width of the tire. The creator mentioned lowering weight in contrast to standard products, expanding resources, and so on.
The Tweel tire was created after extensive testing and development. Modifications to this product’s technology of various kinds have appeared. The delivery of such tires for construction and agricultural machines began in 2012. In the future, more models of similar items with different elastic element configurations will exist.

The benefits and drawbacks
A typical pneumatic wheel has numerous significant benefits over an airless tire with robust inbuilt parts. They are the reason for the growing interest in such structures that has been witnessed thus far.

The primary benefit is enhanced survival. The airless tire lacks an air chamber and is not concerned about punctures. It is likewise not frightened of unintended consequences. Depending on the architecture, operability is maintained even when the supporting structure is severely damaged. Pumping and pressure monitoring are not required, which simplifies operation. It is possible to reject a large and somewhat massive wheel disk. As a result, the entire wheel system is lighter, lowering unsprung mass.
However, several issues prevent such tires from being widely used. First and foremost, there are growing material needs. It necessitates the use of a rubber or polymer with appropriate elasticity, stiffness, and resistance to various stresses. There are additional strict standards for mechanical energy absorption and conversion into heat, followed by dispersion.
All of this complicates and raises manufacturing costs. Furthermore, most tires have a speed limit, which is generally no more than 70-80 km/h. Further acceleration increases mechanical stress and causes unacceptably high temperatures.

Airless tires, unlike pneumatic tires, maintain continuous stiffness and must be changed with new wheels. Simultaneously, dirt ingress into the structure through the open sidewalls might have a negative impact on rigidity and other properties. From these perspectives, pneumatic structures are far more profitable.
As a result, airless tires are now used mostly in light engineering with limited speeds and weights. They are mounted on golf carts, buggies, tiny construction equipment, and other vehicles. Tire manufacture for bicycles, scooters, and other light items has already begun. The availability of bigger samples is currently being debated.